Выбор системы отверстия или вала для той или иной посадки определяется конструктивными, технологическими и экономическими соображениями. Система отверстия является в большинстве случаев предпочтительней, поскольку обуславливает значительное уменьшение номенклатуры режущего и мерительного инструментов, и, следовательно, более экономична по сравнению с системой вала. Однако в отдельных случаях приходиться применять систему вала:
когда заданную точность охватываемой детали (вала, оси) можно обеспечить их калиброванных прутков без обработки резанием;
если имеется несколько соединений с разными по характеру посадками на одном и том же валу;
при использовании в соединениях стандартных изделий, изготовленных по системе вала (шпоночное соединение, соединение наружного кольца подшипника с отверстием в корпусе).
Так же важно правильно выбрать допуски сопрягаемых размеров соединения, поскольку от этого зависит, с одной стороны, качество и долговечность работы соединения, а с другой стороны стоимость и производительность изготовления деталей.
> Выбор посадки с натягом расчетным путем
Расчет посадки с натягом выполняется с целью обеспечения прочности соединения, т.е. отсутствия смещения сопрягаемых деталей под действием внешних нагрузок, а также обеспечения прочности этих деталей в процессесборки соединения. На рисунке 1 изображена схема для расчета посадки с натягом.
Рисунок 2.2.1. - Расчетная схема посадки с натягом.
Величина натяга N, возникающего при сборке соединения, определяется зависимостью:
где N А - деформация растяжения поверхности втулки;
N В - деформация сжатия поверхности вала.
Из задачи определения напряжений и деформаций в толстостенных цилиндрах (задача Ляме) известны зависимости:
где P - давление на поверхности контакта вала и втулки, Па;
D - номинальный диаметр соединения;
E A , E B - модули упругости материала втулки и вала;
C A , C B - коэффициенты, определяемые по формулам:
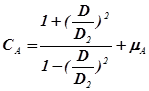
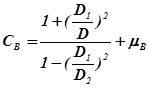
где D1, D2 размеры деталей соединения, м (см. рис. 2.2.1.); A , B - коэффициенты Пуассона.
Из вышеприведенных уравнений следует:
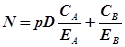
Исходные данные:
D =0.1 м; F= 0.810 3 Н;
D 1 =0м; Е А =2.0610 11 Па;
D 2 = 0.180 м; Е В = 2.0610 11 Па;
L = 0.120 м; T = 2.510 Нм;
А = 0.3; ТА =4.510 8 Па;
В = 0.3; ТВ =4.510 8 Па;
Определяем наименьшее удельное давление на сопрягаемых поверхностях соединения:
где f = 0.14 - коэффициент трения на сопрягаемых поверхностях при сборке соединения с нагревом втулки. Находим наибольшее удельное давление на сопрягаемых поверхностях:
где =0.68 при (L/D) 0.95
Для дальнейшего расчета принимаем меньшее из двух значений: Р max = 122.7*10 6 Па. Определяем коэффициенты C A и C B:
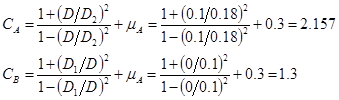
Вычисляем предельные значения натягов N min доп. и N max доп. :

Определяем величину поправки, учитывающей величину смятия микронеровностей поверхностей вала и втулки при сборке соединения:
где К А =К В = 0.6 для стальной втулки и стального вала при сборке соединения c нагревом втулки или охлаждением вала; R ZA =10 мкм; R ZB =10 мкм - высота микронеровностей поверхностей втулки и вала для номинального размера соединения D=100 мм и предполагаемого 7 и 6 квалитета точности деталей соединения. Определяем минимальный и максимальный расчетный натяги:
Рисунок 2.2.2. - Схема расположения допусков.
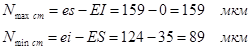
Определяем наибольший и наименьший стандартный натяг:

Определяем эксплуатационный и технологический запас прочности:
Условие N minст N minрасч; N maxст N maxрасч выполнены, эксплуатационный и технологический запасы отличаются не значительно.
> Обоснование посадок всех гладких цилиндрических соединениях
Для гладкого соединения позиция 20/1, 22/1 и 24/1 (проходная крышка - корпус) назначаем посадку H7/h9. Соединение корпуса с крышкой должно быть подвижным и разъемным (с зазором).Поле допуска отверстия принято Н7 из условия посадки подшипника качения. В проходной крышке расположено уплотнение манжетного типа. Для надёжной работы уплотнения манжета должна быть соосна оси вращения вала. Отклонения от соосности вызывают следующие причины: радиальное смещение крышки при сборке относительно отверстия корпуса в пределах посадочного зазора, отклонение от соосности посадочной поверхности под манжету в крышке и оси центрирующей поверхности. Чтобы ограничить радиальное смещение проходной крышки, поле допуска центрирующей поверхности по ГОСТ 18512 - 73 задают h8.
Для соединений 19/1,21/1 и 23/1 (гладкая крышка - корпус) назначаем посадку H7/d11:где Н7 поле допуска отверстия под подшипник, d11 - назначаем исходя из того, что точное центрирование таких крышек по отверстию корпуса требуется.
Соединение 13/2 и 30/4 (кольцо - вал)должно быть подвижным и разъемным. Назначаем посадку D9/k6, такая посадка облегчит установку колеса на вал и произойдет поворот кольца до полного прилегания торцев. При посадке с зазором поворот таких деталей происходит беспрепятственно.
Для соединений 16/2, 14/2, 12/3, 9/3, 11/4 и 10/4 (втулка - вал) назначаем посадку D9/k9.Посадки втулок должны иметь минимальный зазор или минимальный натяг. При большом зазоре втулка превращается в кольцо. При большом натяге усложняется сборка деталей.
Для соединения 5/2 и 8/4 (зубчатое колесо - вал) назначаем посадку H7/u7 - c натягом, чтобы при действии на колесо внешней нагрузки не нарушалось касание сопрягаемых поверхностей, то есть не происходило раскрытие стыка. Для соединений 6/3 и 7/3 назначаем посадку из ряда рекомендуемых H7/m6. Для надежной передачи крутящего момента назначаем переходную посадку. При этом, с назначением переходной посадки в соединении возможен зазор или недостаточный натяг, вследствии чего возникает фрейтинг - корозия, поэтому посадку следует назначать с меньшей вероятностью зазора.
В настоящее время применяют три метода выбора допусков и посадок:
Метод прецедентов (аналогов).
Заключается в том, что конструктор отыскивает в однотипных или других машинах, ранее сконструированных и находящихся в эксплуатации, случаи применения сборочной единицы, подобной проектируемой и назначает такие же или аналогичные допуск и посадку.
Метод подобия.
Является развитием метода прецедентов. Возник в результате классификации деталей машин по конструктивным и эксплуатационным признакам и выпуска справочников с примерами применения посадок. Для выбора допусков и посадок этим методом устанавливают аналогию конструктивных признаков и условий эксплуатации проектируемой сборочной единицы с признаками, приведенными в справочнике.
Общим недостатком этих двух методов является сложность определения признаков однотипности и подобия, в результате чего велика возможность назначения ошибочных допусков и посадок.
Расчетный метод.
Является наиболее обоснованным методом. Выбирая этим методом квалитеты, допуски и посадки при проектировании машин, стремятся удовлетворить эксплуатационно-конструктивные требования, предъявляемые к сборочной единице.
Посадки с зазором
Посадки с зазором предназначены для подвижных и неподвижных соединений.
В подвижных соединениях зазор служит для обеспечения свободы перемещения, размещения слоя смазки, компенсации температурных деформаций, а также компенсации отклонений формы и расположения поверхностей, погрешности сборки и др.
Для наиболее ответственных соединений, которые должны работать в условиях жидкостного трения, зазоры рассчитываются на основе гидродинамической теории трения (для подшипников скольжения). В случаях, когда допускается работа соединения в условиях полужидкостного, полусухого или сухого трения, выбор посадок чаще всего проводится по аналогии с посадками известных хорошо работающих соединений (метод аналогов).
В неподвижных соединениях посадки с зазором применяются для обеспечения беспрепятственной сборки деталей. Их относительная неподвижность обеспечивается дополнительным креплением шпонками, винтами, болтами, штифтами. Выбор посадки в этом случае производится таким образом, чтобы наименьший зазор обеспечивал компенсацию отклонений формы и расположения сопрягаемых поверхностей.
Применение посадок с зазором
Посадки - скользящие. Наименьший зазор равен 0. Установлены во всем диапазоне точностей сопрягаемых размеров (512 квалитеты). Часто применяются для неподвижных соединений с дополнительным креплением при необходимости их частой разборки (сменные детали). В квалитетах 812 могут применяться вместо переходных посадок. Скользящие посадки применяются для центрирования неподвижно соединенных деталей. В подвижных соединениях такие посадки служат для медленных перемещений деталей обычно в продольном направлении; для точного направления при возвратно – поступательном движении; для соединений детали, которых должны легко передвигаться и проворачиваться друг относительно друга при настройке, регулировке или затяжке в рабочее положение. Поскольку получение нулевых зазоров в таких посадках маловероятно, скользящие посадки могут использоваться и для подвижных соединений вращательного движения (при небольших скоростях вращения).
Посадки
- движения. Это посадки с наименьшим
минимальным гарантированным зазором.
Установлены при высоких относительных
точностях изготовления деталей (валы
- 46
квалитетов, отверстия - 57
кв.).
Применяются для особоточных и точных подвижных соединений, в которых требуется обеспечить плавность и точность перемещений чаще всего возвратно – поступательных и ограничить зазор во избежание нарушения соосности, возникновения ударов (при реверсивном движении). При вращательном движении обычно не применяются.
В неподвижных соединениях применяются для обеспечения легкой установки деталей.
Посадки
- ходовые. Характеризуются умеренными
гарантированными зазорами, достаточными
для обеспечения свободного вращения в
подшипниках скольжения. Применяются в
опорах поступательного движения, не
требующих высокой точности центрирования.
В неподвижных соединениях применяются для обеспечения легкой сборки при невысоких требованиях к точности центрирования деталей.
Посадки
- легкоходовые. Имеют значительный
гарантированный зазор, обеспечивающий
свободное вращательное движение при
значительных нагрузках и высоких
скоростях.
В неподвижных соединениях, требующих значительных зазоров при установках и регулировках.
Посадки
-
шарикоходовые. Обладают большим
гарантированным зазором, позволяющим
компенсировать значительные отклонения
расположения сопрягаемых поверхностей
и температурные деформации.
Посадки
- с большими зазорами.
Применяются в основном в грубых квалитетах (11,12) для конструкций малой точности, где большие зазоры необходимы для компенсации отклонений расположения сопрягаемых поверхностей, для обеспечения свободного вращения или поступательного перемещения в условиях запыления и загрязнения.
В отдельных случаях посадки с большими зазорами применяются и в более точных подвижных соединениях (8 и 9 кв.), работающих при особо тяжелых нагрузках или высоких температурах.
Посадки переходные
Переходные посадки предназначены для неподвижных, но разъемных соединений деталей и обеспечивают хорошее центрирование соединяемых деталей. Для них характерна возможность получения, как натягов, так и зазоров. Натяги имеют относительно малую величину и обычно не требуют проверки деталей соединения на прочность, за исключением тонкостенных деталей. Эти натяги недостаточны для передачи соединением значительных крутящих моментов и усилий. Поэтому переходные посадки применяют с дополнительным креплением соединяемых деталей шпонками, штифтами, винтами и др. Такие посадки могут применяться и без дополнительного крепления, когда сдвигающие силы малы, при значительной длине соединения, если относительная неподвижность деталей необязательна.
Зазоры в переходных посадках также невелики, что обеспечивает достаточно высокую точность центрирования.
ЕСДП предусматривает несколько типов переходных посадок, различающихся вероятностью получения натягов или зазоров. Чем больше вероятность получения натяга, тем прочнее посадка.
Переходные посадки установлены в относительно точных квалитетах: валы в 47, отверстия в 58.
Выбор переходных посадок чаще всего производится по аналогии с известными и хорошо работающими соединениями. Расчеты выполняются реже и в основном как проверочные. Они могут включать:
а) расчет вероятности получения зазоров и натягов в соединении;
б) расчет наибольшего зазора по известному допуску соосности;
в) расчет прочности деталей (только для тонкостенных) и наибольшего усилия сборки при наибольшем натяге посадки.
Применение переходных посадок
Посадки
- плотные. Для этих посадок более вероятно
получение зазоров, но возможны и небольшие
натяги. Собираются с применением
небольшого усилия (достаточно деревянного
молотка). Плотные посадки применяются,
если при центрировании деталей допускаются
небольшие зазоры или требуется обеспечить
легкую сборку (сменные детали).
Посадки
- напряженные. Наиболее часто применяемые
переходные посадки. Вероятности получения
зазоров и натягов примерно одинаковые.
Сборка и разборка производится без
значительных усилий (при помощи ручных
молотков). Обеспечивают хорошее
центрирование деталей подвижных узлов
при вращении со средними скоростями.
Посадки
- тугие. Обеспечивают преимущественно
натяг. Вероятность получения зазоров
относительно мала. Применяются для
неподвижных соединений деталей на
быстровращающихся валах с дополнительным
креплением или без него. Применяются
взамен более прочных посадок при
увеличенных длинах соединения или когда
недопустимы большие деформации деталей.
Посадки
- глухие. Наиболее прочные из переходных
посадок. Зазоры практически не возникают.
Для сборки и разборки требуются
значительные усилия: применяются прессы,
распрессовочные приспособления, иногда
термические методы сборки. Разборка
таких соединений производится редко,
только при капитальном ремонте.
Применяются для центрирования деталей
в неподвижных соединениях, передающих
большие усилия, при наличии вибраций и
ударов (с дополнительным креплением).
При небольших нагрузках без дополнительного
крепления.
Посадки с натягом
Посадки с натягом предназначены для неподвижных неразъемных соединений деталей без дополнительного крепления (как правило). Относительная неподвижность деталей достигается за счет напряжений, возникающих в материале деталей вследствие деформации их контактных поверхностей. При прочих равных условиях напряжения пропорциональны натягу. Как правило, посадки с натягом вызывают упругие деформации деталей, но в ряде посадок с большими натягами могут возникать и упруго – пластические деформации.
При одном и том же натяге прочность соединения зависит от материала и размеров деталей, шероховатости сопрягаемых поверхностей, способа соединения деталей и т.д. Поэтому выбор посадки следует производить на основе предварительных расчетов натягов и возникающих напряжений.
Различают следующие основные способы сборки деталей при посадках с натягом:
сборка под прессом за счет его осевого усилия при нормальной
температуре;
сборка с предварительным разогревом охватывающей детали (отверстия) или охлаждением охватываемой детали (вала) до определенной температуры.
Расчет посадок с натягом
Исходными данными для расчета являются:
а) геометрические
размеры:
б)
-
модули упругости вала и втулки.
в)
-
коэффициенты Пуассона.
г)
-
пределы текучести материала вала и
втулки.
Рисунок 3.1 – Расчетная схема соединения с натягом
Условие неподвижности соединения:
(3.1)
где
-
это условная сила, эквивалентная действию
крутящего момента Т и осевой силы
.
(3.2)
-
эквивалентная сила трения, возникающая
за счет натяга.
N = d-D (3.3)
Формула (3) справедлива для идеального случая: абсолютно гладкие и упругие цилиндры.
На основании формулы (3.1), используя выводы задачи Ламэ (это задача определения напряжений и перемещений в толстостенных полых цилиндрах).
где
-
это наименьший, т.е. гарантированный
натяг правильно выбранной посадки с
точки зрения неподвижности.
-
коэффициенты жесткости вала и отверстия,
,
;
-
поправка, учитывающая шероховатость
рабочих поверхностей вала и втулки;
-
учитывает уменьшение натяга за счет
погрешностей формы сопрягаемых
поверхностей;
-
учитывает влияние центробежных сил
(при N<2000об/мин.
);
-
учитывает ослабление натяга при
достижении рабочей температуры;
Вторая часть расчета – проверка прочности соединения.
Условие прочности отверстия (вала):
-
для вала.
где
-
наибольшее давление, которое может
возникнуть в зоне контакта при выбранной
посадке (при
);
-
наибольший натяг при данной посадке.
Применение посадок с натягом
Посадки
- легкопрессовые. Характеризуются
минимальным гарантированным натягом.
Установлены в наиболее точных квалитетах
(валы 4…6, отверстия 5…7). Применяются,
когда крутящие моменты или осевые силы
малы; для соединения тонкостенных
деталей, не допускающих больших
деформаций; для центрирования тяжело
нагруженных и быстровращающихся
крупногабаритных деталей (с дополнительным
креплением).
Посадки
- прессовые средние.
Характеризуются умеренными гарантированными натягами, обеспечивающими передачу нагрузок средней величины без дополнительного крепления. Применяются также в тех случаях, когда применение посадок с большими натягами недопустимо по условиям прочности деталей при тяжелых нагрузках с дополнительным креплением. В этих посадках имеют место упругие деформации деталей. Установлены для относительно точных деталей (валы 5…7, отверстия 6…7 кв.)
Посадки
- прессовые тяжелые.
Характеризуются большими гарантированными натягами. Предназначены для соединений, на которые воздействуют значительные, в том числе и динамические нагрузки. Применяются без дополнительного крепления. В этих посадках возникают упруго – пластические или пластические деформации деталей. Применяются для деталей, выполненных по 7,8 квалитетам.
Расчет переходных посадок на вероятность получения натягов и зазоров
В основу расчета
положено предположение, что размеры
отверстия и вала распределяются по
нормальному закону с центром группирования
в середине поля допуска и средним
квадратным отклонением равным
.
Тогда значения зазора и натяга также
будут распределяться по нормальному
закону симметрично относительно среднего
значения (
).
А вероятность их получения определяется
с помощью интегральной функции вероятности
(z)
Ф(z)
Определяем:
Макс. натяг N=
39 – 0 = 39 мкм = 0,039 мм
Макс.
зазор
=
30 – 20 =10
мкм
= 0,010 мм
Средний натяг
= 14,5 мкм = 0,0145 мм
Допуск отв.
=
30 – 0 = 30 мкм = 0,030 мм
Допуск вала
=
39 – 20 = 19 мкм = 0,019 мм
Определяем среднее квадратное отклонение натяга:
Определяем аргумент интегральной функции (z):
По таблицам по значению Z определяем функцию (z)
Z = 2,41 (2,46) = 0,492
Рассчитываем вероятность натягов (зазоров):
Вероятность натягов
:
,
если
,
если
вероятность зазоров
:
,
при
,
при
=
0,5 + 0,492 = 0,992
99,2 %
=
0,5 – 0,492 = 0,008
0,8 %
Отправить свою хорошую работу в базу знаний просто. Используйте форму, расположенную ниже
Студенты, аспиранты, молодые ученые, использующие базу знаний в своей учебе и работе, будут вам очень благодарны.
Размещено на http://www.allbest.ru/
Р асчет посадок гладких цилиндрических и типовых сое динений
1 . О писание конструкции узла
Заданный узел представляет собой опору вала редуктора с червячным колесом. Опорами являются радиальные однорядные шарикоподшипники /10/ которые наружным кольцом зафиксированы между ступенью стакана /2/ и распорной втулкой /1/, которую поджимает крышка стакана /15/. Стакан /2/ установлен в корпус редуктора /5/. Подшипник /10/ относительно вала зафиксирован с помощью двух болтов которые прижимают пакет деталей относительно оси. В пакет деталей входят: червячное колесо /6/, маслоотбойное кольцо /3/, подшипник /10/.
2 . Р асчет и выбор посадок для гладких цилиндрических соедин е ний
2.1 О пр еделение до пуск а зазора TS , мкм
TS = Sp (max) - Sp (min);
где - максимальное расчетное значение зазора, мкм;
Минимальное расчетное значение зазора, мкм.
2 .2 О пределение квалитет а точности
Сначала определим число единиц допуска, мкм.
aср = TS/2 i (2)
где i - единица допуска, мкм (таблица 2 МУ к КР 07-08 МСС).
Округлим аср до ближайшего меньшего табличного (таблица 3 /8/).
Такому числу единиц допуска соответствует 7 квалитет точности.
2 .3 Округление шероховатости поверхности деталей соединения
Для IT5 … IT10: RZD ? 0,125TD, RZd ? 0,125Td
где TD и Td - допуски отверстия и вала, мкм, по таблице допусков (таблица 3 /8/).
Допуск отверстия и вала по 7 квалитету для диаметра 15 мм равен
TD= Td=18 мкм
RZD=RZd ? 0,125TD ? 0,125·18 ? 2,25 мкм
Принимаем стандартное ближайшее значение шероховатости по таблице (таблица 1 /8/).
RZD =RZd=2,5 мкм
2 .4 Определение пр едельных технологически х зазо ров
В результате приработки зазоры увеличиваются, а натяги уменьшаются, т.к. происходит слияние вершин шероховатости сопрягаемых деталей. При этом высота шероховатости уменьшается на 70% от первоначальной.
Поэтому технологические зазоры определяем по формулам:
Sт (max) = Sp (max) - 1,4·(RZD + RZd); Sт (min) = Sp (min) - 1,4 (RZD + RZd) (4)
приравняем к нулю так как у нас в условии задачи.
2 .5 Назнач ение стандартных п о садок
Для посадок с зазором в системе вала
ch: отверстия EI по условию EI ? Sт (min)
Определение возможной суммы допусков по условиям
ch (TD + Td) ? Sт (max) - EI,
Квалитет точности отверстия может быть больше, чем у вала, но не более чем на два.
ITотв? ITвала, (ITотв. - ITвала)? 2IT (7)
У нас квалитет точности отверстия IT7, а вала IT6 условие выполняется.
По условию задачи у нас система вала (ch) и посадка с зазором поэтому
(TD + Td) ? Sт (max) - EI;
Условие не выполняется поэтому уменьшим допуск вала Td = 11 (IT6)
2 .6 Уточн ение шероховатости поверхности деталей по принятым квалитетам т о ч ности
RZD ? 0,125TD; RZd ? 0,125Td4; (8)
RZD ? 0,125 18? 2,25; RZd ? 0,125 11? 1,375
Выберем стандартные шероховатости по таблице (таблица 1 /8/).
RZD =2,5; RZd =1,60;
2 .7 Назначение завершающего технологического процесс а операции механической о б работ ки
По таблице (таблица 2 Размерная точность и шероховатость изготовления деталей из стали при различных методах обработки) в зависимости от квалитета точности, шероховатости, применения способа обработки и вида поверхности назначаем завершающий технологический процесс обработки поверхности деталей соединения:
Для вала выбираем метод обработки - Тонкое (алмазное).
Для отверстия выбираем метод обработки - Развертывание
Выбираем средства измерения для отверстия и вала (приложение VI /5/), соблюдая условие: ± ? lim ? ± д. Результаты выбора заносим в таблицу.
Таблица 2.1 Выбор средств измерения
2 .8 Проверка услови я правильности выбора полей допусков
Sс (max) ? Sт (max); Sс (min) ?Sт (min);
0,029? 0,033; 0 ?0;
где Sс (max), Sс (min) - максимальные и минимальные зазоры принятой посадки, мкм.
Sс (min) = EI - es; Sс (max) = ES - ei;
Sс (min) = 0 - 0=0; Sс (max) = 0,018 - (- 0,011) = 0,029 ;
2 .9 Схема полей д о пусков соединения
Рисунок 2.1 Схема полей допусков соединения
2 .10 Эскизы соединения и его дет а лей с указанием размеров
Рисунок 2.2 Эскиз соединения
3 . Р асчет и выбор полей допусков для деталей, сопрягаемых с подшипниками качения
3.1 Обоснование характера работы и видов нагружения колец подшипника
цилиндрический соедин е ние подшипник
При выборе посадок подшипников следует учитывать нагрузку, режим работы, класс точности, а также виды нагружения колец подшипника.
Внутренне кольцо подшипника вращается вместе с валом и имеет циркуляционное нагружение.
При таком виде нагружения кольцо воспринимает нагрузку последовательно всей окружностью дорожки качения и передает ёе всей посадочной поверхности вала и поэтому кольцо должно быть неподвижно соединено с валом.
Наружное кольцо подшипника неподвижно установлено в стакан и имеет местное нагружение. При таком виде нагружения кольцо воспринимает нагрузку ограниченным участком окружности дорожки качения и передает её соответствующему ограниченному участку посадочной поверхности стакана. Наружное кольцо должно иметь посадку с небольшим зазором при котором возникают радиальные усилия вращающие кольцо т.е. износ идет по всей поверхности. А если мы посадим с натягом будет износ в одном месте.
3 .2 Выбор стандартного подшипника
Определим номер подшипника. Сперва определим диаметр d внутреннего кольца подшипника. По условию задачи у нас d=35 мм.
то есть 07
Выпишем все стандартные серии подшипников с таким диаметром и соответствующие им значения с (динамическая грузоподъемность подшипника, H) (с. 434-438 /1/).
№ 207 с=25500
№ 307 с=33200
№ 407 с=55300
Теперь определим серию подшипника по критерию интенсивности нагружения. У нас спокойный вид нагружения т.е. нормальный режим работы.
c - динамическая грузоподъемность, kH.
Выразим и вычислим значение c.
0,07 < ? 0,15;
60 < с? 128;
Выберем № 307 подшипник при условии двух подшипников. Проверим выбранный подшипник по критерию интенсивности нагружения.
где С - сумма динамических грузоподъемностей № 307 подшипника
c - динамическая грузоподъемность № 307 подшипника, kH.
С=с+с=66,4 kH;
60 < 66,4 ? 128
Рисунок 3.1 Чёртёж роликового подшипника
Определим все размеры выбранного подшипника (с. 426-430 /1/).
Подшипник № 307
Масса, кг=0,447.
Центриируюшие диаметры, мм
наим. наиб. наим. наиб.
3 .3 Расчет и выбор посадок колец подшипника
Определим предельные размеры вала и отверстия (с.276 /2/).
Предельные размеры вала d и корпуса (стакана).
Предельные размеры внутреннего и наружного кольца подшипника (с.273, с.280 /2/).
dmin = dm + Дm=35 - 0.012=34.988 мм; (17)
Dmin = Dm + ДDm=80 - 0.013=79.987 мм. (18)
Определим интенсивность нагрузки
B - рабочая ширина кольца подшипника;
Bк - конструкторская ширина подшипника, мм;
B=21-2 2,5=21-5=16 мм
Kn - динамический коэффициент. При нагрузке с умеренными ударами и вибрацией, перегрузка 150%, Kn=1;
F - коэффициент учитывающий степень ослабления посадочного натяга при полом вале. Для сплошного вала F=1;
Fn - коэффициент неравномерности распределения интенсивности нагрузки между рядами роликов Fn=1.
Выберем по таблицам (таблицы 9.3; 9.6 с.238 /9/) поля допусков вала и отверстия в зависимости от рассчитанного значения интенсивности нагрузки PR. Для вала - k6; Для отверстия, стакана - H7.
3 .4 Построение схемы расположения полей допусков
Рисунок 2.2 Схема полей допусков а б
Рисунок 2.3 Чертежи деталей контактирующих с подшипником
4 . В ыбор посадки по аналогии
4 .1 Выбор посадки распорной втулки с диаметром d 2=80 мм
Посадка для распорной втулки d2 должна быть с гарантированным зазором для легко снятия и установки, то есть верхнее отклонение распорной втулки должно быть меньше нижнего отклонения стакана. Мы знаем поле допуска стакана H7 (2 задача), подберем под него поле допуска распорной втулки. Выше указанным требованиям соответствует поле допуска распорной втулки g6.
Таким образом получаем посадку в системе отверстия с зазором. Для выбранной посадки приведем схему полей допусков с указанием предельных размеров, отклонений, значений зазоров или натягов.
Рисунок 4.1 Схема полей допусков распорной втулки
4 .2 Выбор посадки маслоотбо й ного кольца d 5=35 мм
Посадка для маслоотбойного кольца должна быть с гарантированным зазором для легкого снятия и установки, то есть нижнее отклонение маслоотбойного кольца должно быть больше верхнего отклонения вала. Мы знаем поле допуска вала k6 (2 задача), подберем под него поле допуска маслоотбойного кольца. Выше указанным требованиям соответствует поле допуска маслоотбойного кольца F8.
Таким образом получаем посадку в системе вала с зазором. Для выбранной посадки приведем схему полей допусков с указанием предельных размеров, отклонений, значений зазоров или натягов.
Рисунок 4.2 Схема полей допусков маслоотбойного кольца
4 . 3 Выбор посадки крышки стакана d 1 = 80 мм
Посадка для крышки стакана d1 должна быть такой чтоб сборка и разборка производились без значительных усилий, то есть верхнее отклонение крышки должно быть меньше нижнего отклонения стакана. Кроме того крышка стакана центрируется не за счёт посадки, а за счёт того что крышка прикручивается к стакану и корпусу. Мы знаем поле допуска стакана H7 (2 задача), подберем под него поле допуска крышки стакана. Выше указанным требованиям соответствует поле допуска крышки стакана f7. Таким образом получаем посадку в системе отверстия с зазором. Для выбранной посадки приведем схему полей допусков с указанием предельных размеров, отклонений, значений зазоров или натягов.
Рисунок 4.3 Схема полей допусков крышки стакана
5 . П осадка шпоночного соединения
5 .1 Определение размеров шпоночного соединения
Размеры шпонки предельные отклонения выбираем в зависимости от диаметра вала (таблица 4.64 /2/)
Таблица 5.1 Основные размеры соединения с призматической шпонкой, мм (по ГОСТ 23360 - 78)
L=23·1.09=25 мм
5 .2 Выбор полей допусков сопрягаемых размеров
Необходимые зазоры и натяги в шпоночном соединении получаются за счет допусков пазов, т.е. принимается система вала. Предельные отклонения находим аналогично заданию 1: ширина 12h9 (-0,043), высота 8h11(-0,090), на длину h14 . Длина шпонки 25h14(-0,520).
5 .3 Расчёт размерных характеристик деталей шпоночного соединения
Выберем свободное соединение (таблица 4.65 /2/), для которого ширина паза вала, ширина паза втулки, длина паза вала. Глубина паза вала, паза втулки, радиусы закругления пазов не менее 0,25 не более 0,4. Отклонения на размеры принимаются по ГОСТ 25347 -89.
Таблица 5.1 Размерные характеристики деталей шпоночного соединения
5 .4 Изображение схемы полей допусков по шир и не шпонки
Рисунок 5.1 Схема полей допусков
5 .5 Выбор средств контроля деталей ра з меров шпоночного соединения
Для дифференцированного контроля размеров деталей шпоночного соединения можно использовать универсальные средства измерения, однако это требует больших, затрат времени. Поэтому на предприятиях автотракторного и сельскохозяйственного машиностроения детали, шпоночных соединений контролируют с помощью предельных калибров.
Ширину пазов валов проверяют пластинами, имеющими проходную и непроходную стороны. Размер от образующей цилиндрической поверхности втулки до дна паза контролируют пробкой со ступенчатым выступом. Глубину паза вала проверяют кольцевыми калибрами. При ремонте машин можно использовать как универсальные средства измерения, так и калибры.
6 . Р асчет размерной цепи
6 .1 Составление размерной цепи
Для узла задано замыкающее звено:
В заданном примере замыкающее звено это зазор между корпусом и червячным колесо. Зазор образуется при затяжке болтов крепления стакана к корпусу, когда стягивается пакет деталей, включающих: стакан подшипников, маслоотбойное кольцо, зубчатое колесо. Суммарный размер этих звеньев по корпусу.
Рисунок 6.1 Схема полей допусков
Общее количество звеньев- 5
Звенья - уменьшающие ()
Звено -уменьшающее ().
6.2 Определение размеров звеньев
где - число увеличивающих звеньев;
Число уменьшающих звеньев.
8=61+38+46-145 8?0
Корректируем размер зубчатого колса до мм, то есть увеличим размер на 8 мм. 8=8
6 .3 Расчет размерной цепи на максимум и минимум
Коэффициент точности размерной цепи (95) /7/:
где - средний коэффициент точности;
Допуск замыкающего звена;
Число звеньев с известными допусками;
Допуски известных звеньев ();
Число звеньев размерной цепи, для которых определяется средний коэффициент точности;
Единица допуска размера звена, выбирается по таблице (таблица 2 /8/)
По таблице (таблица 3 Формулы допусков квалитетов от 5 до 17) соответствует 8 квалитету (25i).
Допуски звеньев по 8 квалитету, кроме корректирующего:
Ступенчатый
Охватываемый
Ступенчатый
Оставляем для корректировки более сложную деталь Д3 так как мы округлили в меньшую сторону.
Определяем допуск для 3 звена
Проводим проверку
Назначение отклонений звеньев:
Размер Д1=61±0,023
Размер Д2=46
Размер Д3=54
Размер Д4=145±0,031
6 .4 Расчет размерной цепи вероятностным методом
Коэффициент точности размерной цепи (236) /5/:
По таблице (таблица 3 Формулы допусков квалитетов от 5 до 17) соответствует IT10 квалитету (64i).
Проверка и корректировка допусков:
Необходима корректировка допусков в сторону уменьшения допусков для звена Д2 как наиболее простого в изготовлении, принимаем допуск по 9 квалитету. При дальнейшем уменьшении допуска равенство не выполняется. Попробуем решить задачу с IT10 на максимум и минимум.
такое невозможно так как >.
Вероятностным методом эту задачу решить невозможно так как у нас на маленький размер дан большой допуск
Результаты расчета размерной цепи сведены в таблицу 6.1
Таблица 6.1 Результаты расчёта размерной цепи
Параметры размерной цепи |
Звенья размерной цепи |
||||||
Обозначение звена |
|||||||
Вид звена |
|||||||
Размер, мм |
|||||||
Единица допуска, мкм |
|||||||
Расчёт на максимум-минимум |
|||||||
Значение допусков,мкм |
|||||||
принятые |
|||||||
Отклонение, мкм |
|||||||
Размеры звеньев с отклонен. |
6 .5 Сравнение результатов расчетов размерной цепи
В результате проделанной работы можно сделать вывод по расчету размерных цепей. Расчет размерных цепей, у которых замыкающее звено имеет большой допуск на размер замыкающего звена, лучше производить методом максимумов и минимумов. А вероятностным метод лучше применять при небольших допусках на размер замыкающего звена.
Б иблиографический список
1. Допуски и посадки: Справочник. В 2-х ч./В.Д. Мягков, М.А. Палей, А.Б. Романов, В.А. Брагинский. - 6-е изд., перераб. и доп. - Л.: Машиностроение, Ленингр. отд-ние, 1982. - Ч. 1. 543 с., ил.
2. Допуски и посадки: Справочник. В 2-х ч./В.Д. Мягков, М.А. Палей, А.Б. Романов, В.А. Брагинский. - 6-е изд., перераб. и доп. - Л.: Машиностроение, Ленингр. отд-ние, 1983. - Ч. 2.448 с., ил.
3. Подшипники качения. Сборник государственных стандартов. Ч.1 -М.: Издательство стандартов, 1989. -439 с.
4. Подшипники качения. Сборник государственных стандартов. Ч.2 -М.: Издательство стандартов, 1989. -432 с.
5. Серый И.С, Взаимозаменяемость, стандартизация и технические измерения. - 2-е изд. , перераб. и доп. - М.: Агропромиздат, 1987. - 367 с.: ил. - (Учебник и учеб. пособие для студентов высш. учеб. заведений)
7. Методические указания. Выбор универсальных средств измерений линейных, размеров до 500 (по применению ГОСТ 8.051-81) РД50-98-86.-М.:Издательство стандартов, 1987. -83 с.
8. МУ к КР 07-08 МСС
9. Взаимозаменяемость, стандартизация и технические измерения: Учебник для вузов/ А.И.Якушев, Л.Н. Воронцов, Н.М. Федотов. - 6-е изд., перераб. и дополн. - М.: Машиностроение, 1987. - 352 с.: ил.
Размещено на Allbest.ru
Подобные документы
Особенности выбора допуска и посадок для гладких цилиндрических соединений, выбор полей допусков для деталей, сопрягаемых с подшипниками качения. Выбор допусков и посадок шпоночных, шлицевых соединений. Расчет допусков размеров заданной размерной цепи.
курсовая работа , добавлен 31.05.2010
Анализ устройства и принципа действия сборочной единицы. Расчет и выбор посадок подшипников качения. Выбор посадок для цилиндрических соединений. Расчет размеров гладких предельных калибров. Точностные характеристики резьбового и зубчатого соединения.
курсовая работа , добавлен 16.04.2011
Определение зазоров, натягов и допусков посадок в гладких цилиндрических соединениях. Расчет посадок в системе основных отверстий, валов, отверстий, гладких предельных размеров калибров. Решение размерных цепей методом полной взаимозаменяемости.
курсовая работа , добавлен 11.07.2015
Назначение посадок для всех сопрягаемых размеров и обозначить их на выданном узле. Расчет посадок для гладких цилиндрических соединений с натягом для заданного соединения. Определение калибров деталей. Схемы расположения допусков резьбового соединения.
курсовая работа , добавлен 28.02.2015
Расчет посадок с зазором в подшипниках скольжения и качения. Выбор калибров для контроля деталей гладких цилиндрических соединений, посадок шпоночных и прямобочных шлицевых соединений. Нормирование точности цилиндрических зубчатых колес и передач.
курсовая работа , добавлен 28.05.2015
Описание сборочной единицы - третьего вала трехступенчатого цилиндрическо-конического редуктора. Анализ гладких цилиндрических соединений. Расчет посадок подшипников качения, посадок для шпоночных, резьбовых и шлицевых соединений, полей допусков.
курсовая работа , добавлен 23.07.2013
Расчет посадок гладких цилиндрических соединений: с натягом и зазором, переходная. Определение параметров размерной цепи. Вычисление посадок подшипников качения, резьбовых и шлицевых, шпоночных соединений. Расчет основных характеристик калибра-скобы.
курсовая работа , добавлен 17.06.2014
Определение точностных характеристик и основных элементов гладких цилиндрических соединений. Выбор посадок с натягом расчетным методом. Определение посадки для подшипника скольжения с жидкостным трением. Обработка данных многократных измерений детали.
курсовая работа , добавлен 16.09.2012
Расчёт гладкого цилиндрического соединения 2 – шестерня – вал. Вычисление калибров для контроля гладких цилиндрических соединений. Выбор нормальной геометрической точности. Определение подшипникового соединения, посадок шпоночного и шлицевого соединения.
курсовая работа , добавлен 27.06.2010
Основные положения, понятия, определения в области стандартизации. Общие сведения, порядок расчета и выбора посадок для подшипников качения. Расчет линейных размерных цепей вероятностным методом. Выбор посадок гладких цилиндрических соединений с зазором.
РАСЧЁТ И ВЫБОР ПОСАДОК
Руководитель
Н. контроль
Студент Барняков В.В.
Группа ММЗ 240006ду-КУ
Каменск-Уральский
Введение 3
Задача 1. Расчет и выбор посадок гладких цилиндрических соединений 5
Задача 2. Расчёт исполнительных размеров гладких предельных калибров 8
Задача 3. Форма и расположение поверхностей 14
Задача 4. Шероховатость поверхности 15
Задача 5. Расчёт посадок подшипников качения 17
Задача 6. Назначение и обоснование посадок резьбового соединении и его
контроль 22
Задача 7. Назначение и обоснование посадок шпоночного и шлицевого
соединений и их контроль 27
Задача 8. Расчёт точности зубчатых колёс и передач и их контроль 35
Задача 9. Расчёт допусков размеров, входящих в размерную цепь 40
Заключение 42
Список литературы 43
Введение
В настоящее время проблемы повышения качества продукции машиностроения наряду с повышением требований к взаимозаменяемости деталей машин при сборке из года в год приобретают все большее значение. Видное место в разрешении этих проблем занимают стандарты, распространяющиеся на допуски и посадки размеров гладких элементов деталей, на их посадки, образуемые при соединении этих деталей, и на калибры, обеспечивающие надежный контроль и взаимозаменяемость деталей, узлов и машин.
Годность деталей с допуском от IT6 до IT17, особенно при массовом и крупносерийном производствах, наиболее часто проверяют предельными калибрами. Этими калибрами проверяют размеры гладких цилиндрических, гладких конических, резьбовых и шлицевых деталей, глубин и высот выступов, а также расположение поверхностей и другие параметры.
Комплект рабочих предельных калибров для контроля размеров гладких цилиндрических деталей состоит из проходного калибра ПР (им контролируют предельный размер, соответствующий максимуму материала проверяемого объекта) и непроходного калибра НЕ (им контролируют предельный размер, соответствующий минимуму материала проверяемого объекта).
С помощью предельных калибров определяют не числовое значение контролируемых параметров, а годность детали, т.е. выясняют, выходит ли контролируемый параметр за нижний или верхний предел, или находится между двумя допустимыми пределами. Деталь считают годной, если проходной калибр (проходная сторона калибра) под действием собственного веса или усилия, примерно равного ему, проходит, а непроходной калибр (непроходная сторона) не проходит по контролируемой поверхности детали. В этом случае действительный размер детали находится между заданными предельными размерами. Если проходной калибр не проходит, деталь является исправимым браком; если непроходной калибр проходит, деталь является неисправимым браком, так как размер такого вала меньше наименьшего допускаемого предельного размера детали, а размер такого отверстая - больше наибольшего допускаемого предельного размера.
При конструировании предельных калибров для гладких, резьбовых и других деталей следует соблюдать принцип подобия Тейлора, согласно которому проходные калибры по форме должны являться прототипом сопрягаемой детали с длиной, равной длине соединения (т. е. калибры для валов должны иметь форму колец), и контролировать размеры по всей длине соединения с учетом погрешностей формы деталей. Непроходные калибры должны иметь малую измерительную длину и контакт, приближающийся к точечному, чтобы проверять только собственно размер детали (что достигается при контроле отверстий, например, микрометрическими нутромерами). Предельные калибры дают возможность контролировать одновременно все связанные размеры и отклонения формы детали и проверять, находятся ли отклонения размеров и формы поверхностей деталей в поле допусков. Таким образом, изделие считают годным, когда погрешности размера, формы и расположения поверхностей находятся в поле допуска.
Изложенные особенности предельных калибров объясняют удобство контроля и предопределили широкое их использование в промышленности при контроле готовой продукции.
Задача 1. Расчет и выбор посадок гладких цилиндрических соединений
Условия задания: Вариант 1
Посадки Ø10H7/e7
1. Построим в масштабе схемы расположения полей допусков сопрягаемых деталей. Масштаб построения схем: в одном миллиметре два микрометра;
Рис 1. Поле допуска для посадки Ø10H7/e7
Рис 2. Поле допуска для посадки Ø10H7/js7
Рис 3. Поле допуска для посадки Ø10H7/s7
Рис 4. Поле допуска для посадки Ø10F7/h7
2. Определим наибольший и наименьший предельные размеры и допуски сопрягаемых деталей. Полученные данные заносим в таблицу 1.
3. Обозначим наибольший, наименьший и средний зазоры и натяги на схемах расположения полей допусков.
4. Определим наибольший, наименьший, средний зазоры или натяги и допуски посадки.
Эскизом для каждого из соединений будет являться сопряжение двух деталей – вала и отверстия. Для контроля отверстия выбираем соответствующую пробку, для контроля вала - скобу (специальный мерительный инструмент, проектируемый для каждого размера) или воспользуемся универсальными мерительными инструментами – штангенциркулем и индикаторной скобой.
Расчёт точности и выбор стандартных посадок для гладких цилиндрических соединений 3
Задача № 1 Обработка прямых однократных измерений 9
Задача № 2. Обработка прямых многократных измерений 9
Задача №3. Обработка косвенных измерений при воспроизводимых условиях 11
Задача № 4. 12
Задача № 5 13
Список использованной литературы 16
Задание № 1
Расчёт точности и выбор стандартных посадок для гладких цилиндрических соединений
1. Определить предельные отклонения, номинальные размеры, допуски для данного сопряжения.
2. Выполнить сему расположения полей допусков заданных посадок с указанием минимальных и максимальных зазоров или натягов.
3. Выполнить эскиз узла (втулки и вала) с заданной посадкой.
4. Выполнить эскизы деталей узла с указанием посадочных размеров.
5. Дать краткую характеристику заданных посадок и где они применяются.
6. Указать систему (СА, СВ), в которой она выполнена.
7. Установить квалитеты деталей соединений.
Исходные данные для задания №1
№№ вар. | Ø сопряжения | |||
Провести расчёт и выбор посадки для гладкого цилиндрического соединения Ø 95Н7/h6 мм .
Посадка в системе отверстия, обеспечивает зазор S max = 57 мкм , S min = 0 мкм .
1. Определяем допуск зазора:
TS = 57 – 0 = 57 мкм .
Число единиц допуска i определяем по таблице: i = 2,17.
а ср
:
TD = Td = –22 мкм .
EI равно нулю, при посадке с зазором поле допуска вала должно располагаться ниже поля допуска отверстия, т.е. предельные отклонения вала будут отрицательные. По таблице находим основное отклонение вала согласно условию es = 0 мкм (основное отклонение h ).
4. Определяем квалитеты отверстия и вала по таблице. Отверстие – седьмой квалитет, вал – шестой (сумма допусков 35+22).
ES = EI + TD = 0 + 35 = + 35 мкм .
Ei = es – TD = 0 – 35 = – 35 мкм .
Записываем выбранную посадку:
S c(max) = D max – d min = 95.035 – 94.978 = 0,057 < 1.76.
S c(min) = D min – d max = 95 – 95 = 0 > -11.236.
Рис. 1. Схема полей допусков соединения
Провести расчёт и выбор переходной посадки для гладкого цилиндрического соединения Ø 95Js8/h7 мм .
Посадка в системе отверстия, обеспечивает натяг N max = 27 мкм , N min = 8 мкм .
1. Определяем допуск натяга:
TN = 27 – 8 = 19 мкм .
Число единиц допуска i определяем по таблице: i = 2,17.
Определяем по таблице и формуле а ср
:
2. Определяем квалитет по таблице – седьмой. Находим допуск седьмого квалитета TD = Td = –35 мкм .
3. Поскольку нижнее отклонение отверстия EI неравно нулю, при переходной посадке поле допуска вала должно частично совпадать с полем допуска отверстия, т.е. предельные отклонения вала будут отрицательные. По таблице находим основное отклонение вала согласно условию es = 0 мкм (основное отклонение h ).
4. Определяем квалитеты отверстия и вала по таблице. Отверстие – восьмой квалитет, вал – седьмой (сумма допусков 54+35).
5. Вторые предельные отклонения равны:
ES = EI + TD = -27+ 54 = + 27 мкм .
Ei = es – TD = 0 – 35 = – 35 мкм .
Записываем выбранную посадку:
Проверить соблюдение условия (1.6).
N c(max) = D max – d min = 95.027 – 94.965 = 0,062 < 1.76.
S c(min) = D min – d max = 94,973 – 95 = -0,027 > -11.236.
Условие соблюдается – посадка выбрана верно.
6. Строим схему полей допусков сопряжения (рис. 1).
Рис. 3. Схема полей допусков соединения
7. Чертим эскизы соединений и его деталей (рис. 4).
Рис. 2. Эскизы соединений и его деталей с обозначением посадки
Провести расчёт и выбор посадки для гладкого цилиндрического соединения Ø 95Н8/s7 мм .
Посадка в системе отверстия, обеспечивает натяг N max = 106 мкм , N min = 17 мкм .
1. Определяем допуск натяга:
TN = 106 – 17 = 89 мкм .
Число единиц допуска i определяем по таблице: i = 2,17.
Определяем по таблице и формуле а ср
:
2. Определяем квалитет по таблице – седьмой. Находим допуск седьмого квалитета TD = Td = 177 мкм .
3. Поскольку нижнее отклонение отверстия EI равно нулю, при посадке с натягом поле допуска вала должно располагаться выше поля допуска отверстия, т.е. предельные отклонения вала будут положительные. По таблице находим основное отклонение вала согласно условию es = 106 мкм (основное отклонение h ).
4. Определяем квалитеты отверстия и вала по таблице. Отверстие – седьмой квалитет, вал – восьмой (сумма допусков 54+177).
5. Вторые предельные отклонения равны:
EN = EI + TD = 0 + 54 = + 54 мкм .
Ei = es – TD = 106 – 177 = – 71 мкм .
Записываем выбранную посадку:
Проверить соблюдение условия (1.6).
N c(max) = D max – d min = 95.054 – 94.929 = 0,125 < 1.76.
N c(min) = D min – d max = 95 – 95.106 = -0.106 > -11.236.
Условие соблюдается – посадка выбрана верно.
6. Строим схему полей допусков сопряжения (рис. 1).
Рис. 5. Схема полей допусков соединения
7. Чертим эскизы соединений и его деталей (рис. 2).
Рис. 6. Эскизы соединений и его деталей с обозначением посадки