Министерство образования и науки Российской Федерации
Государственное образовательное учреждение
высшего профессионального образования
«Кафедра технологии машиностроения, металлообрабатывающие
станки и комплексы»
ОТЧЕТ
по расчетно - графической работе
по дисциплине
«Метрология стандартизация и сертификация»
Расчет и выбор посадок
Аннотация
Расчетно - графическая работа содержит 31 страницы машинописного текста формата А4 , в том числе 9 рисунков источников 5.
В данной работе изложены основные сведения о посадках и произведены соответствующие расчеты, а также подобранны посадки для шпоночного соединения, для шлицевого соединения и рассчитаны исполнительные размеры гладких калибров.
Содержание
Введение ….……………………………………………………………………….3
1. Расчет и выбор посадки с натягом…………………………………………….4
1.1 Назначение посадки с натягом……………………………………………4
1.2 Расчет посадки с натягом………………………………………………….4
2. Назначение и расчет посадок с зазором ………………………………………10
2.1 Назначение посадок с зазором ……………………………………………10
2.2 Расчет посадок с зазором…………………………………………………..10
3. Назначение и расчет переходной посадки……………………………………..14
3.1 Назначение переходной посадки…………………………………………..14
3.2 Расчет переходной посадки ………………………………………………..14
4. Назначение и расчет шпоночного соединения с призматической шпонкой...18
4.1 Назначение шпоночных соединений ……………………………………...18
4.2 Расчет соединения со шпонкой…………………………………………….18
5. Назначение и расчет шлицевых соединений …………………………………..21
5.1 Назначение шлицевых соединений ………………………………………..21
5.2 Расчет шлицевых соединений ……………………………………………...21
6. Назначение и расчет исполнительных размеров гладких калибров ………….26
6.1 Назначение гладких калибров ……………………………………………...26
6.2 Расчет исполнительных размеров гладких калибров …………………….26
6.3 Расчет контролируемого калибра………………………………………….27
7. Заключение……………………………………………………………………….30
8. Список использованной литературы……………………………………………31
2
.
Введение
Посадки с натягом предназначены для неподвижных не разъемных соединений или разбираемых в отдельных случаях соединений при ремонте. В посадках с натягом соединение осуществляется без особых креплений винтами, штифтами, шпонками. При этом относительная неподвижность деталей в посадках достигается за счет напряжений в материале сопрягаемых деталей.
В подвижных соеденениях зазор служит для обеспечения свободы перемещения, размещения слоя смазки, компенсации формы и расположения поверхностей и погрешности сборки. В подвижных соединениях посадки с зазором применяются для обеспечения беспрепятственной сборки деталей. Относительная неподвижность деталей обеспечивается креплением шпонками, болтам, штифтами.
Переходные посадки предназначены для неподвижных, но неразъемных соединений деталей, обеспечивающих хорошее центрирование. Переходные посадки применяют с дополнительным креплением, винтами, болтами, штифтами, шпонками.
Применение шпоночных соединений оправдано лишь в следующих случаях:
- когда по условиям сборки нельзя назначить посадку с натягом, достаточным для передачи заданного вращающего момента;
- когда для передачи заданного вращяющего момента требуется натяг, недопустимый по условиям прочности материала колеса, при этом увеличить размеры соединения не предоставляются возможным.
Шлицевые соединения по сравнению со шпоночными обладают значительными преимуществами, а именно: меньшее число деталей в соединении, значительно большая нагрузочная способность за счет большей площади контакта рабочих поверхностей вала и ступицы, меньшая конценрация напряжений в материале вала и ступицы. Эти преимущества обеспечили широкое распространение шлицевых соединений в автомобильной, тракторной, станкостроительной и других отраслях промышленности.
Калибры - это бесшкальные измерительные инструменты, предназначенные для контроля размеров, формы и расположения поверхностей детали. Применяют калибры двух видов: калибры - скобы - для проверки валов по предельным размерам: калибры - пробки - применяют для контроля отверстий по предельным размерам.
3
.
Изм Лист № докум. Подпись Дата
1. Расчет и выбор посадки с натягом.
1.1 Назначение посадок с натягом
Посадки с натягом предназначены для неподвижных неразъемных (или разбираемых лишь в отдельных случаях при ремонте) соединений деталей, как правило, без дополнительного крепления винтами, штифтами, шпонками и т. п. Относительная неподвижность деталей при этих посадках достигается за счет напряжений, возникающих в материале сопрягаемых деталей вследствие дей¬ствия деформаций их контактных поверхностей. При прочих равных условиях напряжения пропорциональны натягу. В большинстве случаев посадки с натя¬гом вызывают упругие деформации контактных поверхностей, но в ряде посадок с натягом, особенно при относительно больших натягах или в соединениях де¬талей, изготовленных из легких сплавов и пластмасс, возникают упруго-пласти¬ческие деформации (пластические деформации в одной или обеих деталях распро¬страняются не на всю толщину материала) или пластические деформации, распро-страняющиеся на всю толщину материала. Применение таких посадок во многих случаях возможно и целесообразно.
1.2 Расчет посадок с натягом
Расчёт посадок с натягом (посадок с упругой связью) выпол¬няется с целью обеспечить прочность соединения, т. е. отсутствие смещений сопрягаемых деталей под действием внешних нагрузок, и прочность сопрягаемых дета¬лей. Исходя из первого условия, определяется минимальный допу¬стимый натяг , необходи¬мый для восприятия и пере¬дачи внешних нагрузок. Исходя из второго условия, определяет¬ся максимальный допустимый натяг , при котором, как правило, отсутствуют пластиче¬ские деформации. В некоторых случаях прессовые соединения могут надежно работать и при наличии пластических деформаций в наиболее напряженной зоне.
Выбрать стандартную посадку и определить усилие запрессовки без применения термических способов сборки. Мкр = 140 Н.м.
1) Определим минимальное удельное давление на поверхности контакта вала и втулки , Па, возникающее под влиянием натяга. Так как в данном случае соединение нагружено только крутящим моментом, то формула для расчета имеет вид:
4
.
Изм Лист № докум. Подпись Дата
,
где Мкр - вращающий момент, Н.м;
dn - номинальный диаметр соединения, м;
l - длина контакта, м;
f - коэффициент трения.
2) Определим наименьший расчетный натяг Nmin, м, по формуле:
где E1 - модуль упругости материала вала, Па;
E2 - модуль упругости материала втулки, Па;
с1, с2 - коэффициенты Ламе, вычисляемые по формулам:
где d1, d2 - диаметры соответственно вала и втулки, м;
μ1, μ2 - коэффициенты Пуассона.
5
.
Изм Лист № докум. Подпись Дата
3) Определяем значение минимального предельно допустимого натяга:
где γR - поправка на смятие неровностей контактных поверхностей, мкм;
γt - поправка, учитывающая различие температуры среды при сборке и рабочей температуры деталей, мкм;
γц - поправка, учитывающая ослабление натяга под действием центробежных сил, мкм;
γп - добавка, компенсирующая уменьшение натяга при повторных запрессовках, мкм.
Определим поправку на смятие неровностей контактных поверхностей γR:
где Rz1, Rz2 - шероховатости соответственно охватываемой и охватывающей поверхностей, мкм
Определим поправку, учитывающую различие температуры среды при сборке и рабочей температуры деталей:
где α1, α2 - температурные коэффициенты линейного расширения материала деталей, °С-1;
Т1, Т2 - рабочие температуры деталей, °С;
Тср - температура среды при сборке соединения, °С.
Так как рабочие температуры близки к температуре среды, поправка γt=0.
- Определим поправку, учитывающую ослабление натяга под действием центробежных сил.
γц=0.
- Определим поправку, компенсирующую уменьшение натяга при повторных
запрессовках
Так как γп определяется опытным путем, то принимаем γп=10 мкм
6
.
Изм Лист № докум. Подпись Дата
4) Необходимо также обеспечить прочность соединяемых деталей, для этого рассчитаем наибольшее допускаемое давление р, Па, на контактной поверхности, при котором отсутствуют пластические деформации.
Наибольшее допускаемое давление для вала:
где σТ1 - предел текучести материала вала при растяжении, Па.
Наибольшее допускаемое давление для отверстия:
где σТ2 - предел текучести материала отверстия при растяжении, Па.
5) Находим наибольший расчетный натяг N’max, м, при котором возникает :
,
Где -максимально допустимое давление
7
.
Изм Лист № докум. Подпись Дата
6) Уточняем значение максимального расчетного натяга, с учетом ранее найденных поправок:
где γуд - коэффициент, учитывающий увеличение удельного давления у торцов охватывающей детали. По графику (рисунок. 2.2) в зависимости от отношений l/dn и d1/dn принимаем γуд=0,93.
7) По полученным значениям предельно допустимых расчетных натягов подбираем посадку из таблицы 5 ГОСТ25347-82 При этом, для обеспечения работоспособности, необходимо выполнить следующие условия:
По указанной выше таблице выбираем посадку Ø .
8
.
Изм Лист № докум. Подпись Дата
Рисунок 1.1 Схема полей допусков посадки Ø
9
.
Изм Лист № докум. Подпись Дата
2. Назначение и расчет посадки с зазором
Цель расчета посадки с зазором сводится к определению оптимального зазора, Sопт мкм
-для обеспечения жидкостного трения в подшипнике
-для обеспечения свободы перемещения, размешения смазки.
2.1 Назначение посадки с зазором
В подвижных соеденениях зазор служит для обеспечения свободы перемещения, размещения слоя смазки, компенсации температурных деформаций компенсации формы и расположения поверхностей и погрешности сборки, В подвижных соеденениях посадки с зазором применяются для обеспечения беспрепятственной сборки деталей. Относительная неподвижность деталей обеспечивается креплением шпонками, болтами, штифтами.
2.2 Расчет посадки с зазором
1) Определяем величину относительного зазора, φ мкм
Где V- скорость, возникшая в соеденении, м/с.
2)Определяем скорость возникающую в соеденении, V м/с.
где - угловая скорость, рад/с;
-номинальный диаметр соеденения
3)Определяем велечину оптимального зазора в подшипнике, Sопт мкм.
10
.
Изм Лист № докум. Подпись Дата
4) Определяется коэффицент несущей способности, СR
Где µ - динамическая вязкость смазки, ;
Р - среднее удаленное давление Па,
5) Определяется величина среднего удельного давления, Р Па
Где F - радиальная нагрузка, Н;
l - длина контакта, мм
6) Определение величины относительного эксцентриситета подшипника, χ.
7) Определяется минимальная толщина масляного слоя hmin мкм.
Мкм
8) Определяется критическая толщина масляного слоя мкм.
Где - шероховатость поверхности соответственно вала и отверстия мкм.
мкм
Лист
11
.
Изм Лист № докум. Подпись Дата
9) Определяется коэффицент запаса жидкостного трения.
10) Выбор посадки по гост ГОСТ 25347-82. Задавшись системой отверстия
и соответствующим квалитетом (7,8) выбирается посадка удовлетворяющая
следующим условиям.
Указанным условиям удовлетворят посадка
12
.
Изм Лист № докум. Подпись Дата
2.1 Схема полей допусков посадки Ø
13
.
Изм Лист № докум. Подпись Дата
3 Назначение и расчет переходной посадки.
Целью расчета переходной посадки является:
- выбор посадки и определения ее главных характеристик;
- определение вероятностей натяга и зазора
3.1 Назначение переходных посадок
Переходные посадки предназначены для неподвижных, но разъемных со¬единений деталей и обеспечивают хорошее центрирование соединяемых деталей. При выборе переходных посадок необходимо учитывать, что для них характерна возможность получения как натягов, так и зазоров. Натяги, получающиеся в переходных посадках, имеют относительно малую величину и обычно не тре¬буют проверки деталей на прочность, за исключением отдельных тонкостенных деталей. Эти натяги недостаточны для передачи соединением значительных кру¬тящих моментов или усилий. К тому же получение натяга в каждом из собранных соединений без предварительной сортировки деталей не гарантировано. Поэтому переходные посадки применяют с дополнительным креплением соединяемых деталей шпонками, штифтами, винтами и др. Иногда эти посадки применяют без дополнительного крепления, например, когда сдвигающие силы весьма малы, при значительной длине соединения, если относительная неподвижность деталей в соединении не является обязательным условием их качественной работы и т. д.
3.2 Расчет переходной посадки
Где - средний натяг, мкм
- максимальный и минимальный натяг, мкм;
- максимальный и минимальный диаметр вала, мкм
- максимальный и минимальный диаметр отверстия, мкм
14
.
Изм Лист № докум. Подпись Дата
1)Определим максимальный, минимальный и средний натяги в соединении, а также рассчитаем допуски вала и отверстия
ТD , Тd - допуск отверстия и вала мкм
2) Определим среднее квадратичное отклонение натяга по формуле
3) Определим предел интегрирования по формуле
15
.
Изм Лист № докум. Подпись Дата
4) По значению z = -4,025 определяем Ф(-4,025) = 0,0005
5) Рассчитаем вероятность натягов
так как z > 0, то
6) Рассчитаем вероятность зазоров
так как z > 0, то
Следовательно, при сборке примерно 50,05% всех соединений будут с натягом и 49,95% соединений - с зазором.
16
.
Изм Лист № докум. Подпись Дата
3.1 Схема полей допусков посадки Ø18
Лист
17
.
Изм Лист № докум. Подпись Дата
4 Назначение и расчет шпоночного соединения с призматической шпонкой.
Целью расчета является, выбор посадок для шпоночного паза и шпонки, и определение основных параметров соединения.
4.1 Назначение шпоночных соединений
Для соединения деталей машин (зубчатые колеса муфты шкивы рукоятки маховики и т.д.) с валами при невысоких требованиях к точности центрирования применяются шпоночные соединения
Шпонки служат для передачи крутящего момента, для предотвращения проворачивания втулки на валу, для обеспечения перемещения втулки вдоль вала, и для взаимной фиксации в узле
Недостатки шпоночного соединения
- Малая нагрузочная способность
- Ослабление вала шпоночными валами
- Концентрация напряжений узла неблагоприятной формы шпоночных пазов
В машиностроении получили распространение следующие шпоночные соединения
- Призматические шпонки
- Сегментные шпонки
- Клиновые шпонки
- Тангенцальные шпонки
4.2 Расчет соединения со шпонкой
Согласно ГОСТ 23360-78 на диаметр вала 36 мм определить сечение шпонки другие конструктивные параметры
Исходные данные
D=36 мм, Шпонка 36*10*66 Гост 23360-78
Gср=80 Мпа, Iср=100 Мпа.
1.Проверка шпонки по напряжению смятия
18
.
Изм Лист № докум. Подпись Дата
2.Проверка шпонки по напряжению среза
3.Соеденение шпонки с пазом вала.
36 N9 ES=0 36 h11 es=0
EI=-62 ei=-62
N max = ES-EI = 0-(-62)=62 мкм
S max = ES-ei = 0-(-62)=62 мкм
4.Соеденение шпонки с пазом втулки 36 Js9
36 Js9 ES=31
EI=-31
N max = es - EI = 0-(-62) = 62 мкм
S max = ES - ei = 0-(-62) = 62 мкм
19
.
Изм Лист № докум. Подпись Дата
Рисунок 4.1 Схема расположения полей допусков шпоночного соединения
20
.
Изм Лист № докум. Подпись Дата
5. Назначение и расчет шлицевых соединений
Целью расчета является:
- определение вида центрирования;
- определение геометрических параметров соединения;
- выбор посадок и определение основных параметров соединения
5.1 Назначение шлицевых соединений
Шлицевые соединения имеют то же назначение что и шпоночные но обычно применяются при передаче больших крутящих моментов и более высоких требований к соосности соединяемых деталей.
Среди шлицевых соединений, к которым относятся соединения с прямобочными эвольвентными и треугольным профилем зубьев прямобочные прямобочные соединения наиболее распространены. Они применяются для подвижных и неподвижных соединений. В зависимости от передаваемого крутящего момента устанавливается три типа соединений: легкий, средний и тяжелый серии
Способы центрирования:
В шлицевых прямобочных соединениях применяются три способа относительного центрирования вала и втулки: по наружному диаметру (D); по внутреннему диаметру (d); и по боковым поверхностям зубьев (b)
5.2 Расчет шлицевых соединений
1.Шлицевое соединение с параметрами:
b - вид центрирования
z= 10- число зубьев
D=45 мм наружный диаметр
d=36 мм - внутренний диаметр
b= 5 мм толщина зуба
2.Выбор посадки;
Выбор посадки при невысоких требованиях к соосности передачи больших крутящих моментов, а также знака переменных нагрузок
3.Для центрирования по внутреннему диаметру при неподвижном соедении
36
в=10-36
21
.
Изм Лист № докум. Подпись Дата
4.Это обозначение указывает что шлицевое соеденение должно быть образованно при центрировании по внутреннему (d), имеет число зубьев
(10), значение внутреннего диаметра (36) и H11 посадка по внутреннему диаметру, значение наружнего диаметра D=45 Н12, посадка по этому диаметру, значение ширины шлицов (зубьев) в=5мм и посадка по шлицам
5. Центрирование по внутреннему диаметру
36
S max =ES-ei=160-(-620)=-780мкм
S min=es-EI=0мкм
TS=Smax-Smin=-780-0=-780мкм
6 Соединение по наружнему диаметру
S max =ES-ei=250-(-100)=350мкм
S min=es-EI=0мкм
TS=Smax-Smin=350-0=350мкм
7 Соединение по боковым сторонам шлица
5
S max =ES-ei=Dmax-dmin=25-(-6)=31мкм
S min=Dmin-dmax =-6-10=16мкм
TS=Smax-Smin=31-16=15мкм
22
.
Изм Лист № докум. Подпись Дата
Рисунок 5.1 Схема расположения полей допусков посадки 36 (по внутреннему диаметру)
23
.
Изм Лист № докум. Подпись Дата
Рисунок 5.2 Схема расположения полей допусков посадки (по наружному диаметру)
24
.
Изм Лист № докум. Подпись Дата
Рисунок 5.3 Схема расположения полей допусков посадки 5
25
.
Изм Лист № докум. Подпись Дата
6. Назначение и расчет исполнительных размеров гладких калибров
Целью расчета является определить исполнительные размеры калибра пробки и калибра скобы.
6.1 Назначение гладких калибров
Калибры - это бесшкальные измерительные инструменты, предназначенные для контроля размеров, формы и расположения поверхностей деталей. Применяют калибры двух видов: калибр - скобы - для проверки валов по предельным размерам; калибр - пробки - применяют для контроля отверстий по предельным размерам.
6.2 Расчет исполнительных размеров гладких калибров.
2) Исходные данные
= 28.021 мм - наибольший предельный размер отверстия;
= 28.000 мм - наименьший предельный размер отверстия;
Н=0.004 мм - допуск на изготовление калибра - пробки с цилиндрической измерительной поверхностью;
z=0.0035 - отклонение середины поля допуска на изготовление проходного калибра пробки относительно контролируемого отверстия;
y= 0.003 - допустимый выход размера изношенного калибра - пробки за границу допуска контролируемого изделия.
3)Проходной новый
Р - ПРисп = (+z+0.5Н)-н
Р - ПРисп = (25.000+0,003+0,5*0,004)-0,004
4) Проходной изношенный
Р - ПРизн = - y
Р - ПРизн = 28.000 - 0,003= 27,997
5) Непроходной
Р - НЕисп = (+ 0,5Н)-н
Р - НЕисп = (28,021 + 0,5 *0,004)-0,004
1.1) Расчитать калибр - скобу для отверстия 36s6 (+0.059/+0.043)
1.2) Исходные данные
=36.059 мм - наибольший предельный размер вала;
= 36.043 мм - наименьший предельный размер вала;
Н1 = 0.004 мм - допуск на изготовление калибра пробки с цилиндрической измерительной поверхностью;
z1 = 0.0035 мм - отклонение середины поля допуска на изготовление проходного калибра - пробки относительно контролируемого отверстия;
26
.
Изм Лист № докум. Подпись Дата
у1 = 0.003 - допустимый выход размера изношенного калибра - пробки за границу допуска контролируемого изделия.
Нр = 0.0015 мм - допуск на изготовление контрольных калибров для контроля калибра - скобы.
1.3 Проходной новый.
Р - ПРисп = (d - z - 0.5Н1)+н
Р - ПРисп = (36.059 - 0.0035 - 0.5 *0.004)+0,004=36.0535)+0,004
1.4 Проходной изношенный.
Р - ПРизн = + у1
Р - ПРизн = 36.059 + 0003 = 36.062
1.5 Непроходной.
Р - НЕисп = (dmin - 0.5Н1)+н1
Р - НЕисп = (36.043 - 0.5*0.004)=36.041+0.004
6.3 Расчет контролируемого калибра
1. Проходной новый.
К - ПРисп = (- z + 0.5Нр)-нр
К - ПРисп = (36.059 - 0.0035 - 0.5 *0.004)-0,0015=36.0535)-0,0015
2 Проходной изношенный.
К - ПРизн = (+ у1+ 0.5Нр)-нр
К - ПРизн = (36.059 + 0.003+0.5*0,0015)=36.0627-0,0015
3 Непроходной.
К - НЕисп = (dmin++ 0.5Нр)-нр
К - НЕисп = (36.043 + 0.5*0,0015)=36.04375-0,0015
Рисунок 6.1 Схема расположения полей допусков исполнительного размера калибра пробки.
Рисунок 6.1 Схема расположения полей допусков исполнительного размера калибра скобы.
Заключение
В расчетно - графической работе были рассмотрены и рассчитаны основные типы посадок применяемых в машиностроительных и станкостроительных производствах, а также были выполнены эскизы основным узлов и деталей.
Список использованной литературы
Радкевич Я.М. Cтиртладзе А.Г., Лактионов Б.И., Метрология стандартизация и сертификация: Учеб. Для ВУЗов - Москва:. Высш. Шк. 2007.-800с.
Лифиц И.М. Стандартизация, метрология и сертификация: Учебник - М.: Юрайт - издат,2004 . - 296с.
Сергеев А.Г. Метрология, стандартизация, сертификация. А.Г. Сергеев М.В.Латышев В.В. Терегеря - Москва: Логос, 2005 - 356 с.
Допуски и посадки. Справочник. Под. Ред. В.Д. Мягкова - М.: Машиностроение. 1982.-567с.
Стандарты систем. ОНВ, ЕСТП, ЕСДП, ЕСКД, ЕСТД, ГСС, ГСИ.
Скачать: У вас нет доступа к скачиванию файлов с нашего сервера.
Выбор различных посадок для подвижных и неподвижных соединений можно производить на основании предварительных расчетов, экспериментальных исследований или ориентируясь на аналогичные соединения, условия работы которых хорошо известны.
Посадки с зазором. Рассмотрим один из вариантов расчета посадки подшипника скольжения.
Известно, что при гидродинамическом режиме работы масляный клин в подшипнике скольжения возникает только в области определенных зазоров между цапфой вала и вкладышем подшипника. Поэтому задачей настоящего расчета является нахождение оптимального расчетного зазора и выбор по нему стандартной посадки.
Рассмотрим упрощенный метод расчета и выбора посадок, изложенный в .
Толщина масляного слоя в месте наибольшего сближения поверхностей отверстия и вала ,
где S – диаметральный
зазор;
- относительный эксцентриситет;
е – абсолютный эксцентриситет вала в подшипнике при зазоре S.
Принципиальный график зависимости толщины масляного слоя от величины зазора S приведен на рис.2.7.
К
Рис.2.7. График
зависимости толщины масляного слоя от
зазора
K(R ZD +R ZD + g) =
K(4Ra D +4Rad+ g),
где К2 – коэффициент запаса надежности по толщине масляного слоя; g – добавка на неразрывность масляного слоя ( g = 2 - 3 мкм).
Поэтому необходимо соблюдать условие
h , S min , (2.1)
где – минимальный допустимый зазор, при котором толщина масляного слоя равна допустимой .
Относительный эксцентриситет х min , соответствующий зазору S min , из-за возможности возникновения самовозбуждающихся колебаний вала в подшипнике рекомендуется принимать не менее 0,3, т.е. x min 0,3.
Для определения х используем полученную в зависимость
,
(2.2)
где - угловая скорость вала, рад/с; С R – коэффициент нагруженности подшипника; P – среднее удельное давление (Па),
.
Здесь F r – радиальная нагрузка на цапфу, Н; l, d H.C. – длина подшипника и номинальный диаметр соединения, м;- динамическая вязкость смазочного масла при рабочей температуре t n (Hс/м 2),
,
(2.3)
где t и –
температура испытания масла (50°С или
100°С);– динамическая вязкость при t и =
50 o C
(или
100 о С); n –
показатель степени, зависящий от
кинематической вязкости масла(табл.2.2).
Таблица 2.2
Значения показателей степени n в уравнении (2.3)
Обозначив
,
из формулы (2.2) получим
.
(2.4)
На рис. 2.8 приведены зависимости А от х и отношения l/d H.C . Для определения х min необходимо по формуле (2.4) определить Аh, соответствующее :
.
По рис. 2.8 можно определить х min – относительный эксцентриситет, соответствующий зазору ;х опт и А опт – относительный зазор и параметр А, соответствующие оптимальному зазору S опт, при котором толщина масляного слоя достигает своего наибольшего значения h / (см.рис.2.7); А х – значение параметра А при х = 0,3.
Минимальный допустимый зазор
,
где К - коэффициент, учитывающий угол охвата (табл.2.3).
Максимальный допустимый зазор при h =
.
Таблица 2.3
Коэффициенты, учитывающие угол охвата
Угол охва-та |
Отношение l/d НС |
|||||||||||
При выборе посадки необходимо выполнить условие
S max . (2.5)
где
-
поправка, связанная с различием
коэффициентов линейных расширений
материалов вала и втулки или существенным
различием температур соединенных
деталей,.
Здесь D ,
d
– коэффициенты линейного расширения
втулки и вала; t D ,
t d
- разность между рабочей и нормальной
(20 0 С)
температурами;
-
поправка, связанная с наличием неровностей
на поверхностях вала и втулки,
=8(Ra D
+ Ra d); Т изн – допуск на
износ.
Величина допуска на износ может задаваться числовым значением, рассчитанным по требуемой долговечности подшипника, или определяться по предписанному коэффициенту запаса точности К Т:
,
При выборе посадки необходимо использовать дополнительное условие, по которому средний зазор S C в посадке должен быть примерно равен оптимальному S опт:
.
Если при выборе посадки не удается выполнить условия (2.1) и (2.5), то следует произвести проверку правильности выбора посадки теоретико-вероятностным методом, определив для этого вероятностные зазоры:
;
.
При невыполнении
условий
и
необходимо
провести повторный расчет.
Рекомендации по применению некоторых посадок с зазором. Посадку Н5/h4 (S min = 0 и S max = Td +Td) назначают для пар с точным центрированием и направлением, в которых допускается проворачивание и продольное перемещение деталей при регулировании. Эти посадки можно использовать вместо переходных (в том числе для сменных частей). Для вращающихся деталей их применяют только при малых скоростях и нагрузках.
Посадку Н6/h5 назначают при высоких требованиях к точности центрирования (например, пиноли в корпусе задней бабки токарного станка, измерительных зубчатых колес на шпинделях зубоизмерительных приборов), посадку Н7/h6 (предпочтительную) - при менее жестких требованиях к точности центрирования (например, сменных зубчатых колес в станках, корпусов под подшипники качения в станках, автомобилях и других машинах, поршня в цилиндре пневматических инструментов, сменных втулок кондукторов и т. п.). Посадку Н8/h7 (предпочтительную) назначают для центрирующих поверхностей, когда можно расширить допуски на изготовление при несколько пониженных требованиях к соосности.
Посадки Н5/g4; Н6/g5 и Н7/g6 (последняя предпочтительная) имеют наименьший гарантированный зазор из всех посадок с зазором. Их применяют для точных подвижных соединений, требующих гарантированного, но небольшого зазора для обеспечения точного центрирования (например, золотника в пневматической сверлильной машине, шпинделя в опорах делительной головки, в плунжерных парах и т. п.).
Для подвижных посадок наиболее распространены Н7/f7 (предпочтительная), Н8/f8 и подобные им посадки, образованные из полей допусков квалитетов 6, 8 и 9.
Посадки Н7/е8, Н8/е8 (предпочтительные), Н7/е7 и посадки, подобные им, образованные из полей допусков квалитетов 8 и 9, обеспечивают легкоподвижное соединение при жидкостной смазке. Их применяют для быстровращающихся валов больших машин.
Посадки Н8/d9, Н9/d9 (предпочтительные) и подобные им посадки, образованные из полей допусков квалитетов 7, 10 и 11, применяют сравнительно редко. Например, посадку Н7/d8 используют при большой частоте вращения и малом давлении в крупных подшипниках, а также в сопряжении поршень - цилиндр в компрессорах, посадку Н9/d9 - при невысокой точности механизмов.
Посадки Н7/c8 и Н8/с9 характеризуются значительными гарантированными зазорами, используются для соединений с невысокими требованиями к точности центрирования. Наиболее часто эти посадки назначают для подшипников скольжения (с различными температурными коэффициентами линейного расширения вала и втулки), работающих при повышенных температурах (в паровых турбинах, двигателях, турбокомпрессорах, турбовозах и других машинах, в которых при работе зазоры заметно уменьшаются вследствие того, что вал нагревается и расширяется больше, чем вкладыш подшипника).
При выборе посадок (на основе расчета) необходимо учитывать отношение l/d: чем меньше это отношение, тем меньше должен быть наименьший зазор.
Переходные посадки. Переходные посадки Н/js, Н/k, Н/m, Н/n используют в неподвижных разъемных соединениях для центрирования сменных деталей или деталей, которые при необходимости могут передвигаться вдоль вала. Эти посадки характеризуются малыми зазорами и натягами, что, как правило, позволяет собирать детали при небольших усилиях (вручную или с помощью молотка). Для гарантии неподвижности одной детали относительно другой соединения дополнительно крепят шпонками, стопорными винтами и другими крепежными средствами.
Переходные посадки предусмотрены только в квалитетах 4 - 8. Точность вала в этих посадках должна быть на один квалитет выше точности отверстия.
В переходных посадках при сочетании наибольшего предельного размера вала и наименьшего предельного размера отверстия всегда получается наибольший натяг, при сочетании наибольшего предельного размера отверстия и наименьшего предельного размера вала - наибольший зазор.
Посадки с натягом. Посадки с натягом предназначены в основном для получения неподвижных неразъемных соединений без дополнительного крепления деталей. Иногда для повышения надежности соединения дополнительно используют шпонки, штифты и другие средства крепления, как, например, при креплении маховика на коническом конце коленчатого вала двигателя. Относительная неподвижность деталей обеспечивается силами сцепления (трения), возникающими на контактирующих поверхностях вследствие их деформации, создаваемой натягом при сборке соединения.
Рассмотримобщий случай расчета посадок с натягом,
когда соединение состоит из полого вала
и втулки (рис. 2.9).
Разность между
диаметром вала и внутренним диаметром
втулки до сборки определяет натяг N.
При запрессовке деталей происходит
растяжение втулки на величинуN D и одновременно сжатие вала на величинуN d ,
причем N =N D +N d .
Из зада-чи определения напряжений и
перемещений в толстостенных полых цилиндрах (задачи Ламе)
известны зависимости N D = pC 1 /E 1 ;
N d = pC 2 /E 2 .
Cложив почленно эти равенства и выполнив
простые преобразования, получаем
N = pd НС [(С 1 /E 1) + (C 2 /E 2)],
где N - расчетный натяг; р - давление на поверхности контакта вала и втулки, возникающее под влиянием натяга; d НС - номинальный диаметр сопрягаемых поверхностей; Е d и Е D – модули упругости материалов соответственно охватываемой (вала) и охватывающей (отверстия) деталей, Па; С d и C D –коэффициенты Ламе, определяемые по формулам
;
,
где d 1 – диаметр отверстия полого вала,м ;d 2 – наружный диметр охватывающей детали, м; d и D – коэффициенты Пуассона соответственно для охватываемой и охватывающей деталей. Для сплошного вала (d 1 = 0) C d = 1 - d ; для массивного корпуса (d 2 ∞) C D = 1 + D .
Расчет посадок с натягом производят в следующем порядке:
По значениям внешних нагрузок – осевой силы, крутящего момента (F a , T K) и размерам соединения (d H.C , l) определяется требуемое минимальное давление (Па) на контактных поверхностях соединения:
при действии Т К
;
при действии F a
;
при действии Т К и F a
,
где F a – продольная осевая сила, стремящаяся сдвинуть одну деталь относительно другой, Н; Т К – крутящий момент, стремящийся повернуть одну деталь относительно другой, Нм; l – длина контакта сопрягаемых поверхностей, м; f - коэффициент трения при установившемся процессе распрессовки или проворачивания (табл.2.4).
Таблица 2.4
Коэффициенты трения для материалов
По полученным значениям определяется необходимое значение наименьшего расчетного натяга N min (м), который должен обеспечить передачу крутящего момента и осевой силы:
.
3. Определяется
величина минимального допустимого
натяга с учетом поправок к
,
то есть
где ш – поправка, учитывающая смятие неровностей контактных поверхностей деталей при образовании соединения;
ш = 1,2 (R zd + R zD) = 5 (R ad + R aD),
где t – поправка, учитывающая различие рабочей температуры деталей (t D и t d) и температуры сборки (t сб), различие коэффициентов линейного расширения материалов соединяемых деталей ( D и d),
ц – поправка, учитывающая ослабление натяга под действием центробежных сил (существенна для крупных быстровращающихся деталей); для сплошного вала и одинаковых материалов соединяемых деталей
.
Здесь V – окружная скорость на наружной поверхности втулки, м/с;- плотность материала. Поправка ц для стальных деталей диаметром до 500 мм, вращающихся со скоростью до 30 м/с, не учитывается; n – добавка, компенсирующая уменьшение натяга при повторных запрессовках, определяется опытным путем.
Определяется максимальное допустимое удельное давление , при котором отсутствует пластическая деформация на контактных поверхностях деталей. В качестве P max берется наименьшее из двух значений
;
,
где Тd и ТD – предел текучести материалов охватываемой и охватывающей деталей.
Устанавливается наибольший расчетный натяг (м)
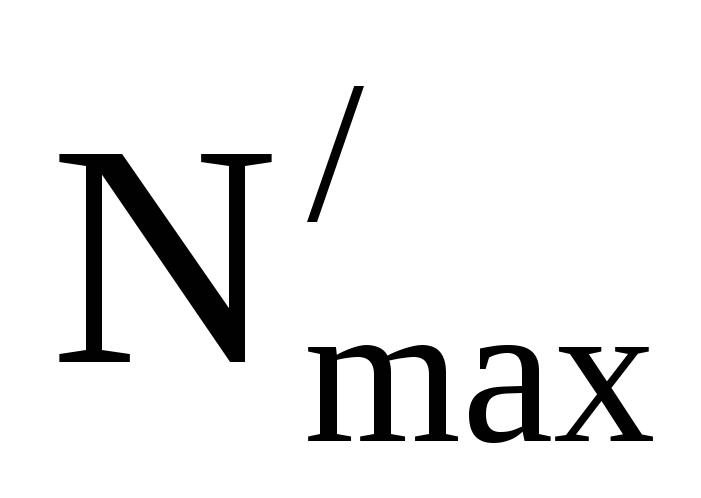
г
0,9
0,2
0,5 ; 0,6; 0,7
0,8
де уд – коэффициент увеличения удельного давления у торцов охватывающей детали, принимается по графику (рис.2.10); t – температурная поправка, учитываемая, если при рабочей температуре натяг увеличивается.Выбирается посадка из таблиц системы допусков и посадок с соблюдением следующих условий: максимальный натяг N max в подобранной посадке должен быть не больше [N max ], т.е.N max [N max ]; минимальный натяг
N min в подобранной посадке должен быть больше [N min ], т.е.N min [N min ].
Рассчитывается необходимое усилие при запрессовке собираемых деталей по формуле
F n = f n P max d H.C l,
где f n – коэффициент трения при запрессовке; f n = (1,15-1,2)f; P max – удельное давление при максимальном натяге (N max),
.
Рекомендации по применению некоторых посадок с натягом. Посадки Н/р; Р/h – "легкопрессовые" - характеризуются минимальным гарантированным натягом. Установлены в наиболее точных квалитетах (валы 4 - 6-го, отверстия 5 – 7-го квалитетов). Применяются в таких случаях, когда крутящие моменты или осевые силы малы или случайное относительное смещение деталей несущественно для их служебной роли; для соединения тонкостенных деталей, не допускающих больших деформаций; для центрирования тяжелонагруженных или быстровращающихся крупногабаритных деталей (с дополнительным креплением).
Посадки H/r; H/s; H/t и R/h; S/h; T/h – "прессовые средние " - характеризуются умеренными гарантированными натягами в пределах (0,0002 – 0,0006)d НС, обеспечивающими передачу нагрузок средней величины без дополнительного крепления. Установлены для относительно высоких точностей деталей (валы 5 – 7-го, отверстия 6 – 7-го квалитетов). Сборка соединений возможна как под прессом, так и способом термической деформации.
Посадки H/u; H/ x; H/z и U/h – "прессовые тяжелые " - характеризуются большими гарантированными натягами (0,001 – 0,002)d НС. Предназначены для соединений, на которые воздействуют тяжелые, в том числе и динамические нагрузки. Применяются, как правило, без дополнительного крепления соединяемых деталей. Сборка обычно осуществляется методом термической деформации. Для посадок с большими натягами предусмотрены относительно широкие допуски деталей (7 – 9-го квалитетов).
Задача: выбрать посадку распорной втулки на вал диаметром 32 мм, провести вероятностный расчет посадки.
Основным назначением распорной втулки является фиксация размера между подшипником качения и зубчатым колесом. Особых требований по точности сопряжения предъявлять нет надобности, соединение должно собираться легко, поэтому назначаем посадку для данного соединения Ø32Н9/d9 .
Рассчитываем предельные размеры отверстия Ø32Н9.
По ГОСТ 25346-89 «Основные нормы взаимозаменяемости. Единая система допусков и посадок. Общие положения, ряды допусков и основных отклонений» определяем значениядопуска IT9 = 62 мкми основного (нижнего) отклоненияEI = 0 мкм.
Верхнее отклонение будет равно
ES = EI + IT9 = 0 + 62 = +62 мкм.
Предельные размеры отверстия:
D min = D 0 + EI = 32,000 + 0 = 32,000 мм;
D max =D 0 + ES = 32,000 +0,062 = 32,062 мм.
Рассчитываем предельные размеры вала Ø32d9 .
По ГОСТ 25346 определяем значениядопуска IT9 = 62 мкми основного (верхнего) отклоненияes = -80 мкм.
Нижнее отклонение будет равно
ei = es – IT9 = – 80 – 62 = – 142 мкм.
Предельные размеры вала:
d min = d 0 + ei = 32,000 – 0,142 = 31,858 мм;
d max = d 0 + es = 32,000 – 0,080 = 31,920 мм.
Результаты расчётов оформим в виде таблицы.
Таблица 1
Расчёт предельных размеров сопряжения
Размер |
IT , мкм |
ES (es), |
EI (ei), |
D min (d min ), |
D max (d max ), |
Строим схему расположения полей допусков сопрягаемых деталей и рассчитываем предельные значения зазоров.
Рис.2. Схема расположения полей допусков вала и втулки
S max = D max – d min = 32,062 – 31,858 = 0,204 мм ;
S min = D min – d max = 32,000 – 31,920 = 0,080 мм .
Средний зазор
S cp = (S max + S min )/2 = (0,204 + 0,080)/2 = 0,142 мм.
Допуск посадки
T S = IT D + IT d = 0,062 + 0,062 = 0,124 мм .
Принимаем, что и размеры вала, и размеры распорной втулки распределены по нормальному закону, и центр группирования каждого из размеров совпадает с координатой середины поля допуска. При нормальном распределении параметра 99,73% всех значений попадают в диапазон, ограниченный значением 6 стандартных отклонений (± 3σ ). Если мы примем, что данный диапазон равен допуску (Т = 6σ ), то на долю несоответствующих единиц продукции будет приходиться 0,27% деталей, что для условий машиностроительного производства является приемлемым. Следовательно, стандартное отклонение значений нормируемого параметра можно рассчитать по приближенной формуле как шестую часть допуска:
d = Т d /6,
D = Т D /6.
Тогда стандартное отклонение посадки получим путем геометрического суммирования стандартных отклонений размеров вала и втулки:
.
Так как зазор – разность между диаметрами втулки и вала, то при распределении размеров в партии деталей по нормальному закону сами зазоры также будут распределены по нормальному закону. Центр группирования зазоров будет соответствовать среднему значению зазора. Таким образом, предельные значения вероятных зазоров можно получить как
S max. вер . = S cp + 3 S ;
S min. вер . = S cp – 3 S .
Рассчитаем предельные значения вероятных зазоров.
;
Рис.3. Схема распределения вероятных зазоров сопрягаемых деталей
S max.вер. = 142 + 3 14,6 = 185,8 мкм 0,186 мм;
S min.вер. = 142 – 3 14,6 = 98,2 мкм 0,098 мм.